Are you looking to add a touch of style and functionality to your vehicle? Fabricating your own running boards could be the perfect solution.
Not only do they enhance the look of your ride, but they also offer practical benefits like easier access and added protection. Imagine stepping into your vehicle with ease, while also setting it apart with custom-made features. This guide will walk you through the process, ensuring you have all the knowledge and confidence needed to create running boards that suit your taste and needs.
Ready to get started? Let’s dive into the details and transform your vehicle together.
Materials And Tools
Creating running boards requires basic materials and tools. Essential items include metal sheets, a welding machine, and measuring tape. Drills, saws, and screws are also needed for assembly.
Creating running boards for your vehicle can be a rewarding DIY project. It’s essential to start with the right materials and tools to ensure the process goes smoothly. Choosing the right supplies not only saves time but also enhances the durability and aesthetic appeal of your running boards.Essential Materials
The first step is selecting the materials for your running boards. Consider using aluminum or steel as they offer strength and durability. Aluminum is lightweight and resistant to rust, making it a popular choice. Steel, on the other hand, provides a robust and sturdy option, perfect for heavy-duty use. Rubber or plastic trims are often added to enhance grip and provide a finished look. These materials ensure safety and style, as they prevent slipping and can complement the design of your vehicle. Don’t forget about protective coatings. Adding a layer of paint or powder coating can prevent corrosion, especially if you live in a region with harsh weather conditions. This extra step can extend the life of your running boards significantly.Required Tools
Having the right tools can make or break your fabrication project. You’ll need a drill and drill bits suitable for metal. These are crucial for making precise holes for screws and bolts. A saw is necessary to cut the metal sheets to your desired size and shape. A measuring tape is your best friend for ensuring accuracy in dimensions. Accurate measurements prevent the frustration of having to redo parts of your project. Safety gear is non-negotiable; wear gloves and goggles to protect yourself from sharp edges and metal filings. A welding machine might be required if you’re working with steel. Welding provides strong joints but requires practice and caution. Have you ever thought about how welding could change your DIY skills? It’s a tool that can open up a world of possibilities in metalwork. Lastly, a screwdriver set is essential for assembling the running boards and securing them to your vehicle. Using the right screwdriver ensures tight fittings and a professional finish. Taking the time to gather these materials and tools will set you up for success. Have you checked your toolbox lately? Make sure you’re equipped to tackle this project with confidence and precision.Design Considerations
Crafting running boards involves precise design considerations for durability and style. Choose materials that withstand weather and weight. Ensure the design complements the vehicle’s look while providing safe footing.
Designing running boards for your vehicle can be a rewarding project that enhances both function and style. It’s crucial to focus on design considerations that ensure the running boards are not only aesthetically pleasing but also practical. This involves choosing the right size and selecting the appropriate material type. These elements can significantly affect the durability and usability of the running boards.Choosing The Right Size
Selecting the correct size for your running boards is essential for safety and appearance. Measure the length of your vehicle’s side where the board will be installed. Consider the width as well; it should be wide enough for a comfortable step but not too wide to look bulky. Think about who will use the running boards. Are they for young children or elderly family members? This can influence the height and width to ensure ease of use. A friend of mine learned this the hard way when his boards were too narrow, making them difficult to use.Selecting The Material Type
The choice of material impacts the running board’s weight, durability, and look. Common materials include aluminum, steel, and plastic. Aluminum is lightweight and resistant to rust, making it a popular choice. Steel, while heavier, offers excellent strength and durability. It can handle more weight but may require more maintenance to prevent rust. Plastic is cost-effective and lightweight but may not be as durable as metal options. Ask yourself what conditions your running boards will face. Will they be exposed to harsh weather or heavy loads? This will help you decide on the most suitable material. My first set of running boards were plastic, and they couldn’t withstand the wear and tear of daily use, teaching me the importance of selecting the right material. Design considerations are crucial in ensuring your running boards are both functional and stylish. Have you thought about the size and material that best suits your needs?Cutting The Material
Begin by measuring the running board dimensions carefully. Precision in cutting the material ensures a perfect fit. Use the right tools to slice through metal or plastic smoothly, avoiding rough edges.
Crafting your own running boards can be a rewarding project, but it all starts with cutting the material correctly. Precision in cutting ensures a snug fit and a professional appearance. Whether you’re tackling this task for the first time or refining your skills, this section will guide you through the essentials of cutting the material effectively.Measuring Accurately
Before you start cutting, accurate measurements are crucial. Measure twice, cut once—this is a mantra worth repeating. Use a tape measure to gauge the exact length and width needed for your running boards. Consider the vehicle’s specific dimensions and any design elements you want to include. Jot down the measurements clearly. This is where a small miscalculation can lead to wasted material and effort.Using Cutting Tools
Selecting the right cutting tools is as important as the measurements themselves. A circular saw or a jigsaw can be ideal for most materials used in running boards. Ensure your blades are sharp to avoid jagged edges. Safety goggles and gloves aren’t optional; they protect you during the process. Think about the cutting surface. A stable table or workbench prevents material from slipping, leading to cleaner cuts. Ever tried using a dull blade? It’s a frustrating experience that teaches the importance of tool maintenance. Always check your equipment before starting. Cutting the material is a hands-on part of fabricating running boards. It demands attention to detail and the right tools. What challenges have you faced in cutting projects, and how did you overcome them?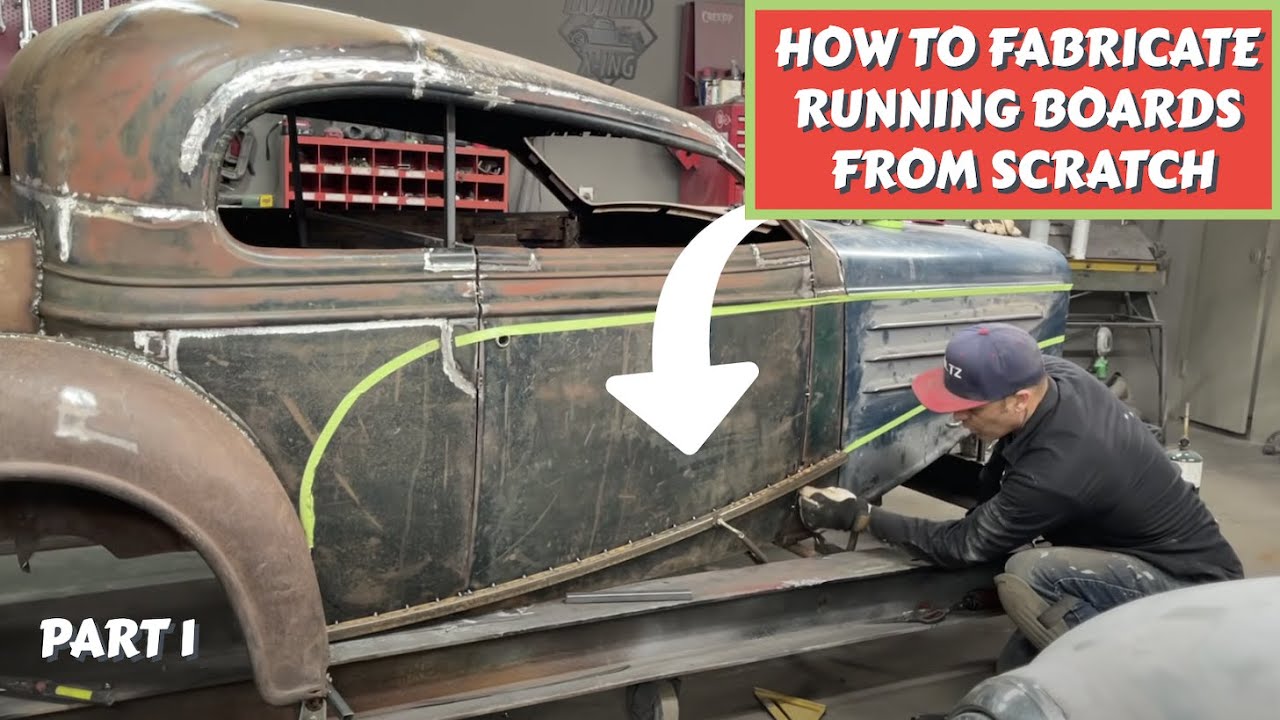
Credit: www.youtube.com
Shaping And Forming
Crafting running boards involves shaping and forming metal or plastic to fit vehicle contours. Start by measuring the vehicle’s side steps. Cut and bend materials accordingly. Ensure precision for a snug fit. Secure the boards with brackets and screws, providing stability and durability.
Shaping and forming running boards is where your creativity meets craftsmanship. It’s not just about bending metal; it’s about turning raw materials into functional art. This stage is crucial as it determines the aesthetic and functionality of your running boards. You may wonder, how do you transform a flat piece of metal into a curved, sleek component that complements your vehicle? Let’s dive into the methods that can help you achieve those bespoke shapes and forms.Bending Techniques
To start shaping your running boards, mastering bending techniques is essential. Whether you are using manual tools or high-tech machinery, the process requires precision and patience. One common method is using a sheet metal brake, which allows you to create sharp, clean bends at specific angles. If you’re working with thicker materials, consider using a hydraulic press brake. It provides the power needed to bend tougher metals without compromising on accuracy. Have you ever tried using heat to make bending easier? A propane torch can soften metal enough to bend it smoothly without causing stress fractures. Remember, the key is to maintain even heat distribution to avoid weak spots.Creating Custom Shapes
Once you have the bending down, the next step is crafting custom shapes. This is where your running boards can truly stand out. Templates can be your best friend here. By tracing a design onto your material, you ensure that each piece is uniform and precise. Are you aiming for curves or unique angles? Using a jig or mold can help maintain consistency while shaping. These tools hold your material in place, allowing you to focus on achieving the desired form. Don’t be afraid to experiment with different designs. Personalizing your running boards not only enhances their appearance but can also improve their fit and function. Engage with your project by asking yourself: What shape best complements your vehicle’s body style? Consider how different shapes will impact the ease of stepping in and out of the vehicle. The right shape can add a touch of elegance or a rugged appeal, depending on your preference. Fabricating running boards is not just about following a process; it’s about enjoying the journey of creation. By understanding and applying bending techniques and experimenting with custom shapes, you can craft running boards that are not only practical but also uniquely yours.Welding And Assembly
Fabricating running boards requires precision and skill. Welding and assembly are critical steps in this process. Proper execution ensures durability and safety. Let’s delve into the essentials of welding and assembling running boards.
Welding Basics
Welding is crucial in fabricating running boards. It joins metal parts securely. Choose the right welding technique for your material. MIG welding is popular for its ease and speed. It uses a wire electrode to create strong bonds. Always clean metal surfaces before welding. Dirt and rust weaken welds. Ensure proper ventilation in your workspace. Welding produces harmful fumes.
Wear protective gear at all times. Gloves, masks, and goggles shield from sparks and heat. Keep a fire extinguisher nearby. Safety is paramount in welding.
Assembling The Components
After welding, assemble the running board components. Start by aligning the pieces accurately. Use clamps to hold them in place. Double-check all alignments. Misalignment leads to uneven boards.
Use bolts and nuts for added security. They reinforce welded joints. Tighten all connections securely. Loose parts compromise safety. Test the assembly for stability. Apply weight to check sturdiness. Inspect every connection point thoroughly.
Finally, clean the assembled running board. Remove any debris or metal shavings. A clean product enhances appearance and performance.

Credit: www.amazon.com
Finishing Touches
Crafting running boards involves precise measurements and sturdy materials. Cut metal or wood to fit vehicle dimensions. Secure brackets and bolts for stability, ensuring a polished finish enhances both functionality and style.
When you’ve invested time and effort into fabricating running boards, the finishing touches are essential to ensure durability and visual appeal. This part of the process is where attention to detail truly makes a difference. Whether you’re enhancing the look of your vehicle or protecting the boards from wear and tear, these steps will help you achieve a professional finish.Sanding And Smoothing
Begin by inspecting your running boards for any rough edges or uneven surfaces. Use sandpaper with a medium grit to gently smooth these areas. This step not only enhances the appearance but also ensures a better surface for coatings to adhere to. Once the initial sanding is complete, switch to a finer grit sandpaper. This will give the boards a polished finish, making them smooth to the touch. Remember, the smoother the surface, the better the final result will look. Think back to a time you admired a vehicle’s running boards. Was it the sleek, smooth finish that caught your eye? Achieving this is well within your reach with some careful sanding.Applying Protective Coatings
With the surface prepped and smooth, it’s time to add protective coatings. These coatings defend against rust, scratches, and environmental damage. Choose a high-quality primer as your base layer to ensure longevity. After the primer, apply a durable paint or powder coating. This not only protects but also allows you to customize the boards to match your vehicle’s aesthetic. Consider how a bold color or a sleek black finish could enhance your car’s overall look. Don’t forget the final layer of clear sealant. This acts as a barrier against moisture and UV rays, keeping your running boards looking new for longer. Imagine the satisfaction of seeing your hard work withstand the test of time and elements. As you finish these steps, ask yourself: How does this attention to detail change the way you view your project? These finishing touches are not just about aesthetics; they’re about ensuring your running boards serve you well for years.Installation Process
Running boards enhance vehicle accessibility and style. Installing them requires careful planning. Follow these steps to ensure a smooth installation process.
Preparing The Vehicle
Start by securing your vehicle on a flat surface. Engage the parking brake. This ensures safety during installation. Clean the undercarriage thoroughly. Dirt and debris can obstruct the installation. Gather all necessary tools and materials. This includes wrenches, bolts, and brackets. Check the running boards for any defects. Ensure they match your vehicle’s specifications.
Mounting The Running Boards
Locate the mounting points beneath the vehicle. These are usually pre-drilled holes. Align the brackets with these points. This ensures a snug fit. Secure the brackets using bolts. Tighten them with a wrench. Double-check the alignment before proceeding. Place the running boards onto the brackets. Ensure they are level and aligned. Use additional bolts to secure them firmly. Inspect the installation for stability. Test the running boards by stepping on them. Ensure they hold weight without shifting.
Safety Tips
Fabricating running boards requires careful attention to safety. Ensuring a safe environment can prevent accidents and injuries. Proper precautions protect you and your work. Prioritize safety at each step of the process.
Handling Tools Safely
Always wear protective gear when working with tools. Safety goggles and gloves are essential. Ensure your workspace is well-lit and organized. This reduces the risk of accidents. Keep tools sharp and in good condition. Dull tools can slip and cause harm.
Read the manual of each tool before use. Know the function and limits of your tools. Never rush through a task. Take your time to work safely and efficiently.
Ensuring A Secure Fit
A secure fit is crucial for running board safety. Measure twice before cutting any materials. Precision prevents errors and ensures a snug fit. Use clamps to hold materials steady during fabrication. This prevents slipping and improves accuracy.
Test fit your running boards before final installation. Make any necessary adjustments to ensure stability. Double-check all fastenings and supports. A secure attachment keeps the running boards safe and reliable.
Common Mistakes
Fabricating running boards involves common mistakes such as incorrect measurements and neglecting proper safety gear. Mistakes in material choice can also compromise durability. Ensure precise planning to avoid these errors.
Fabricating running boards can be a rewarding project for any DIY enthusiast. But it’s easy to trip over common mistakes that can turn a fun project into a frustrating ordeal. Understanding these pitfalls can save you time, money, and a lot of headaches.Avoiding Measurement Errors
One of the most frequent mistakes is inaccurate measurements. Imagine cutting your materials only to realize they don’t fit. Measure twice, cut once—it’s a saying for a reason. Use a reliable measuring tape and double-check your numbers. Always account for the thickness of the materials you’re using. A friend once trimmed his boards perfectly, only to find they were too thick for the mounting brackets. That extra quarter-inch matters.Preventing Material Damage
Material damage often happens due to mishandling or using the wrong tools. Have you ever scratched a surface you just polished? Use protective coverings on your workspace to prevent scratches and dents. Select the right tools for cutting and sanding. A dull blade can tear your materials instead of giving a clean cut. Investing in quality tools pays off in the long run, both in terms of time and the quality of your finished product. Have you considered the type of material you’re working with? Different materials have different tolerances. Metal requires different handling compared to wood or plastic. Knowing your material well can help you avoid these pitfalls. What mistakes have you encountered in your DIY projects? Learning from others can be just as valuable as learning from your own experiences.Credit: corporate.lippert.com
Conclusion
Fabricating running boards can be a rewarding project. You need patience and basic tools. Start by planning your design carefully. Measure the vehicle accurately. Cut the materials with precision. Assemble all parts securely. Ensure safety and durability. Test the boards before use.
This project boosts your creativity. It also saves money. You can customize the boards to fit your style. Enjoy the process and the final result. Share your work with friends or online. Your DIY skills improve with practice. Have fun and build confidence in your abilities.